Balcony Waterproofing: Top Techniques and Materials
by Christina
- October 9th, 2024 /
- Education,Waterproofing
Without proper balcony waterproofing, water can threaten a building’s structural integrity, property value, and the health of its occupants. Exterior structures like balconies face continued exposure to the elements and are more prone to water damage, which leads to structural deterioration, corrosion, and mold.
Modern waterproofing techniques and high-quality materials prevent costly water infiltration, effectively protecting structural integrity, safeguarding asset values, enhancing aesthetic appeal, and providing a healthy and safe environment. With minimal interruptions during installation and relatively low ongoing maintenance, effective balcony waterproofing helps property owners avoid costly reconstruction or repair bills to appreciate the full value of their investment.
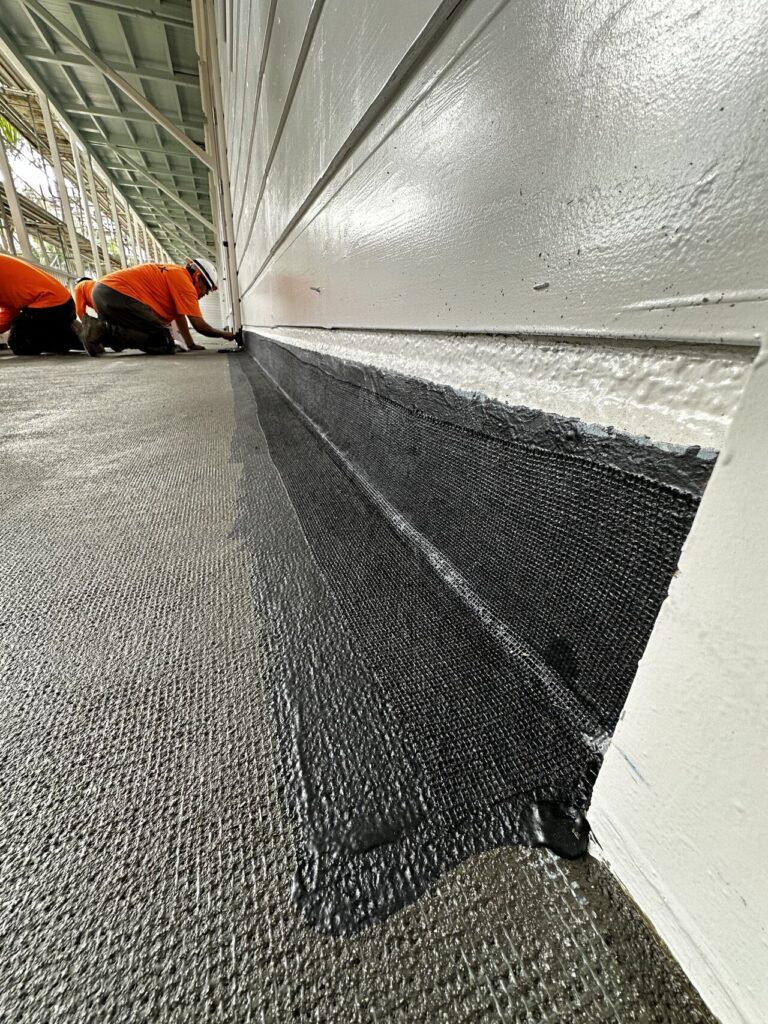
Understanding Balcony Waterproofing Requirements
Before any waterproofing techniques can be applied, the existing structures must be evaluated for strength, soundness, and stability. It’s recommended that professional building inspectors assess the structure in question to ensure that the project adheres to local building regulations. Once those requirements have been met, the installation process can commence.
Assessment
Knowledgeable inspectors, contractors, and installation experts evaluate the current balcony conditions to determine what repairs (if any) must be completed to provide the waterproofing system with a durable structural base. In extreme cases, the assessment may reveal widespread water damage that requires complete renovation, but for relatively new balcony constructions, repairs are typically minimal, if at all necessary.
The substrate must be structurally sound, free from mold, and sloped to prevent water from pooling. Experts will also determine which balcony waterproofing system best addresses the expressed needs and existing structure to provide the most value.
Building Codes and Regulations
Each state and city upholds numerous building codes and regulations designed to ensure balconies comply with approved dimensions, load-bearing capacities, structural requirements, and railing specifications.
Relevant regulations include but are not limited to:
- AC39 – Acceptance Criteria For Walking Decks
- California codes SB 721 and SB 326
Regarding waterproofing, these regulations further stipulate characteristics of compliant drainage systems and substrate slopes to properly direct water away from the structure. Balcony waterproofing methods must also comply with fire rating regulations, volatile organic compounds (VOCs), and the wildland-urban interface.
Balcony Waterproofing and Construction Phases
Waterproofing can occur at multiple stages of balcony construction. Each stage requires a slightly modified approach to accommodate various challenges, but every phase of construction presents an opportunity to build a waterproof balcony that’s designed to last.
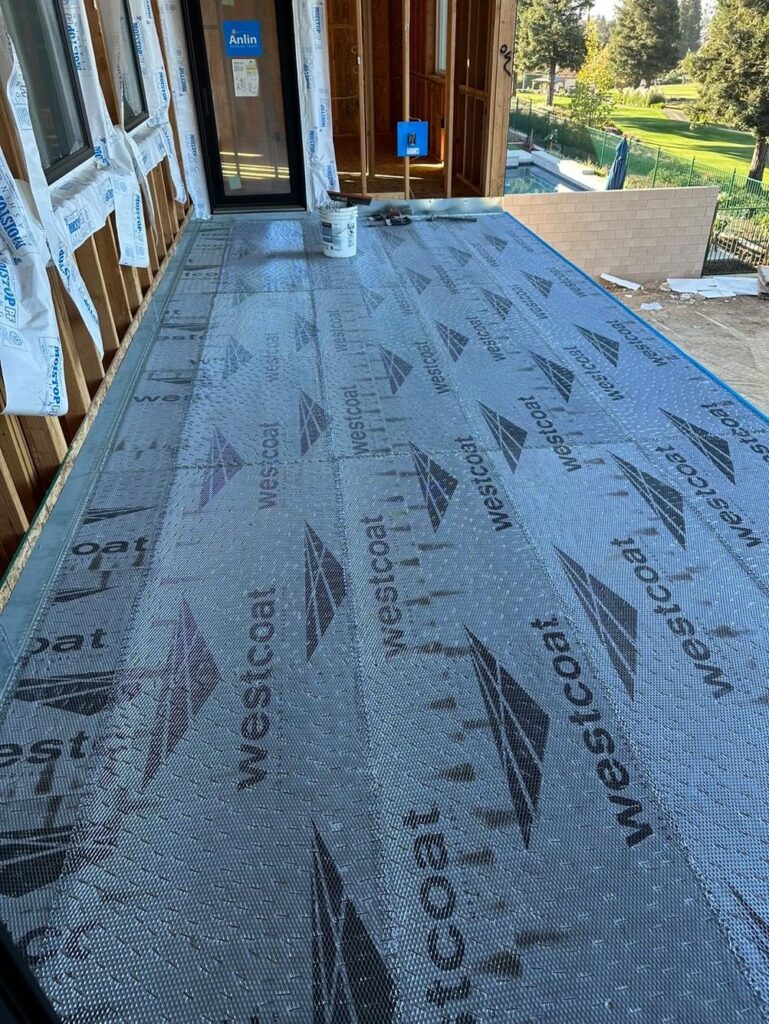
New Construction
Waterproofing balconies during new construction maintains the initial property investment and ensures structural integrity for years to come. This ideal approach seamlessly and proactively integrates the project with modern compliance with local building regulations. It also allows for the selection of the most up-to-date waterproofing method and corresponding installation products such as full-system solutions. Proper installation and maintenance safeguards any balcony’s durability, strengthens property values, and minimizes repair costs.
Existing Construction
Although waterproofing balconies on existing construction can marginally impact building occupants, liquid, or cementitious waterproofing methods ensure that disruptions are kept to a minimum, thanks to fast-drying, low odor. Depending on the total number of balconies that require waterproofing, applications can be compartmentalized, or completed in waves or sections to maintain efficiency. With an investment in balcony waterproofing, property owners can also minimize future repairs or renovations that can further disrupt tenants’ and property maintenance budgets.
Renovations
Compliance with local building codes and regulations remains at the forefront of any balcony waterproofing application, including during renovations. An assessment of the existing structure allows contractors and installation experts to recommend a particular waterproofing method — such as liquid or cementitious coatings — based on the factors involved. Balcony waterproofing can also be applied following the scheduling of other trade work to ensure efficiency and minimize interruptions.
Maintenance and Repairs
Ongoing maintenance is essential to preserve a balcony’s integrity and ensure long-term durability. Property managers and building owners should schedule regular inspections to identify early signs of wear and tear, such as cracks, pooling water, or peeling waterproof membranes. In some cases, installation experts can apply sealants, caulking, waterproof tape, polyurethane, and other waterproofing techniques in outdoor areas to extend a balcony’s lifespan until more thorough repairs can be made, but it’s important to remember that these are only temporary solutions.
Regular cleaning and resealing are essential maintenance practices for balcony waterproofing systems. This process involves thoroughly cleaning the surface and applying an additional layer of topcoat. The fresh topcoat acts as a protective barrier, shielding the waterproof membrane from UV rays, moisture, and daily wear and tear. By resealing periodically, you not only enhance the appearance of the balcony but also significantly extend the lifespan of the entire waterproofing system.
If your assessment reveals a more substantial issue, though, you may need to consider more extensive repairs to prevent long-term structural damage, such as those described above.
Types of Balcony Waterproofing Methods
Multiple balcony waterproofing methods incorporate the proper materials for the intended application and expected results. Several factors influence the selected balcony waterproofing method, from the desired aesthetic finish and existing structural components to the proposed budget and environmental conditions.
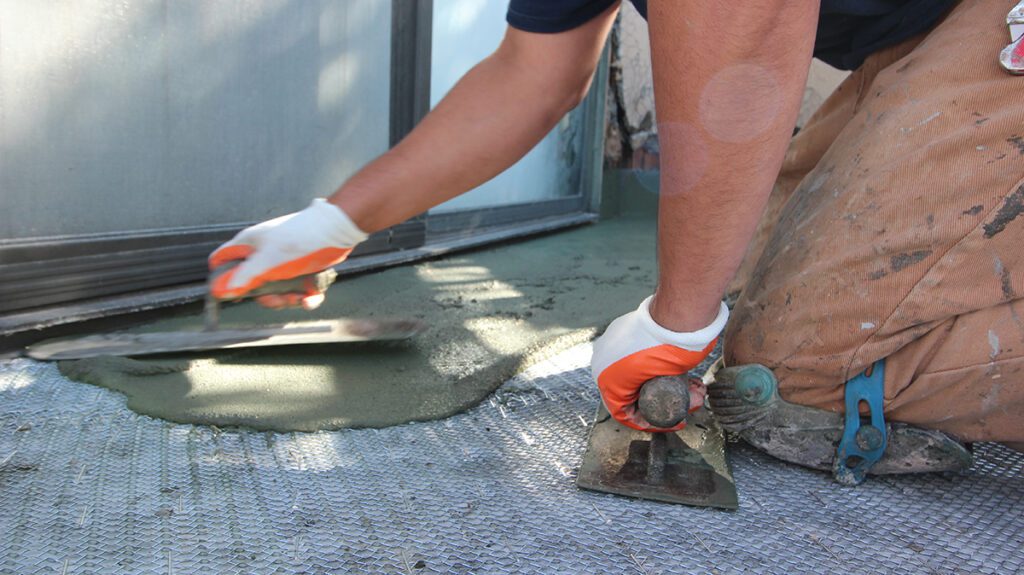
Liquid Waterproofing Membranes
Often comprised of acrylics, polymer-modified asphalts, or polyurethanes, liquid waterproofing membranes are a popular solution for concrete structures, including balconies.
As the liquid membrane spreads across the balcony surface, it expands into pores and minor cracks to create a monolithic protective coating. This adaptive waterproofing method easily conforms to complex layouts to reduce materials and labor otherwise spent on such irregularities. Liquid waterproofing membranes also adjust to minor structural movements caused by varying temperature differentials and environmental conditions.
Westcoat offers WP Wrap as a supplemental part of the ALX and MACoat full-system solutions. Made with flexible flashing fabric, this latex, asphalt-modified waterproofing membrane incorporates an antimicrobial component to ward off mold and mildew around the edge of a balcony while the lath and waterproof coatings do the heavy lifting. The seamless, reinforced waterproof membrane can be finished with a slurry coat, cementitious coating, or Westcoat’s SC-10 Acrylic Topcoat.
Sheet Membranes
For a more uniform and consistent approach to waterproofing, sheet membranes provide a continuous layer that also resists punctures or tears. Sheet membranes are ideal for larger balconies, as the oversized sheets can efficiently and effectively cover a wider area. These pre-fabricated sheets — made from polyethylene, vinyl, EPDM, or bituminous materials — are compatible with concrete, wood, metal, and tile balcony structures.
Westcoat incorporates sheet membranes into the ALX waterproofing system for plywood installations. After preparation procedures, the sheet membrane establishes a backup waterproofing measure to ensure balconies remain watertight. Additional balcony waterproofing materials are then applied to protect the balcony’s structural integrity for many years.
Cementitious Waterproofing
In terms of efficiency and cost, cementitious waterproofing delivers immense value. Waterproofing additives are incorporated into the blend of sand and cement used to finish a balcony, integrating waterproofing properties while enhancing the aesthetic appeal.
Cementitious waterproofing methods work well with substrates made from concrete or plywood and can easily be applied to basic balcony designs in climates with minor temperature fluctuations. With that said, we do see these coatings installed effectively in a variety of climates.
Polyurethane Waterproofing
Polyurethane waterproofing is flexible and can fill in small cracks and imperfections. The robust glossy finish is durable, resistant to UV rays, and provides long-lasting protection against moisture and wear. However, creating the ideal aesthetic appeal requires several applications and compounding curing times. Should any moisture be present in the substrate before application, the trapped moisture can lead to blistering that negates any benefits the polyurethane waterproofing offers. Among balcony waterproofing methods, polyurethane waterproofing is fairly well-known, but it can actually be the least effective and the most time-consuming as a standalone waterproofing technique.
Full-System Solutions from Westcoat
The ALX and MACoat waterproofing systems offered by Westcoat and installed by our Qualified Contract Applicators (QCAs) address waterproofing needs across multiple levels and applications to ensure existing structures can adequately resist water infiltration. Full system solutions from Westcoat provide property owners with lower long-term maintenance and repair bills for years after installation.
Underlying each Westcoat waterproofing system is a proven process that establishes a robust barrier between water and the existing structures. The efficacy of the selected waterproofing system requires thorough surface preparation before it can be applied. Post-installation, routine quality inspections proactively identify and address slight concerns to maintain the waterproofing layer’s integrity.
Westcoat’s ALX and MACoat waterproofing solutions can also be applied at various construction stages to ensure the longevity of balconies and their surrounding structures. From assessment to installation and in compliance with local building codes and regulations, Westcoat waterproofing systems establish a strong base upon which property owners need only to perform minor maintenance. Our innovative, durable solutions supply confidence by ensuring high-quality materials and workmanship from start to finish.
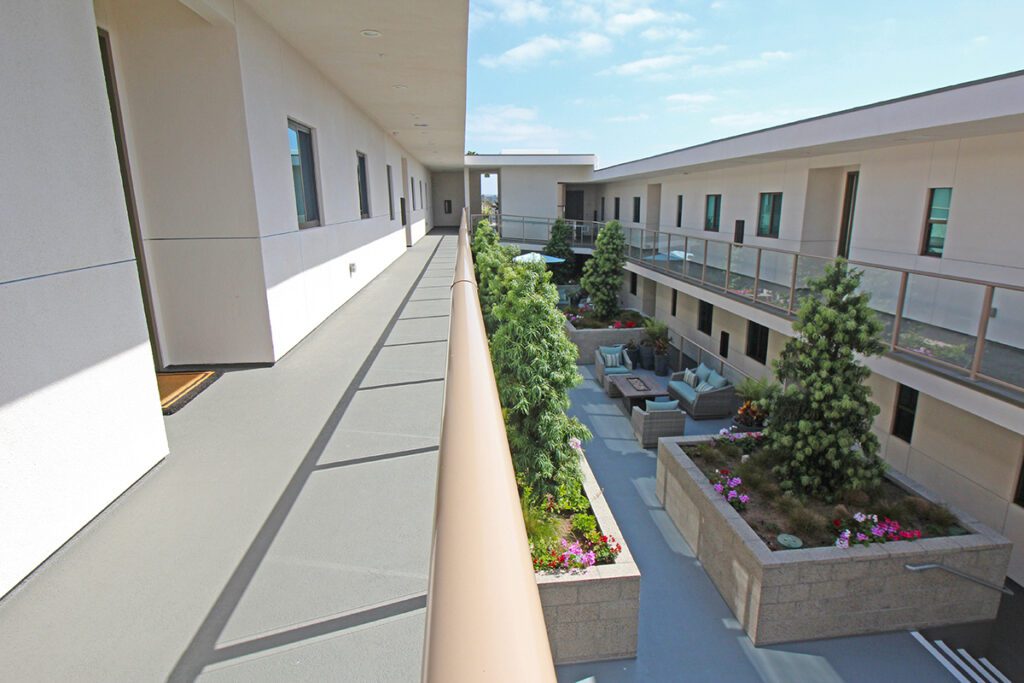
ALX
The ALX waterproofing system provides property owners and architects with a vibrant palette of standard and custom finishes that pair effortlessly with available patterns to achieve a wide variety of aesthetic appeals. Compatible with plywood balconies, this cost-effective system delivers strength and durability while also incorporating sound reduction qualities. Westcoat’s ALX waterproofing solution is ideal for larger balconies that require an element of flexibility and benefit from UV and skid resistance.
The Westcoat ALX waterproofing system creates a durable, concrete-like finish through a multi-layer process that includes a sheet membrane, metal lath, base coat, slurry coat, texture coat, and top coat, all applied using polymer-modified cementitious techniques. QCAs may also incorporate polyurethane sealant and seam tape as supplemental components to ensure a watertight seal and finish the entire process with Westcoat’s SC-10 Acrylic Topcoat to ensure a professional and appealing result.
Beyond these numerous benefits, the Westcoat ALX waterproofing system remains compliant with Class A and One-Hour fire ratings, the City of Los Angeles Residential Code and Building Code regulations, and Wildland Urban Interface Requirements. Review the ALX Standard CSI specifications, explore our ALX Waterproofing System brochure, or find an applicator in your area to learn more.
MACoat
Beyond the versatility, durability, and value the ALX waterproofing system provides, the permeable MACoat waterproofing solution extends similar benefits to address heavy-duty applications. High-traffic areas demand an extremely durable and low-maintenance solution that complies with building regulations and promises longevity. Westcoat’s MACoat waterproofing system checks each of these boxes, offering architects, property owners, and commercial builders multiple color options that seamlessly mesh with existing or proposed designs.
The MACoat waterproof system consists of a fiber lath, base coat, slurry coat, optional texture coat, and topcoat. Individual waterproofing methods — such as epoxy patch gels, polyurethane sealants, seam tape, and waterproofing resin — may be used to address challenging areas that require a custom solution, but they may impact the physical appearance of the system. A layer of SC-10 Acrylic Topcoat seals the low-odor and low-VOC, UV-resistant waterproofing system so it remains comfortable underfoot.
Explore the MACoat Standard CSI specifications and our high-resolution MACoat waterproofing system brochure, or contact us if you have any additional questions. Our team of knowledgeable experts can help direct you to the best waterproofing solution possible for your particular project.
Additional Balcony Waterproofing Techniques
The balcony’s condition and any issues found during the assessment may require extra waterproofing to create a strong, impermeable seal that better protects it against water damage. Standard solutions include sealants, the addition of or adjustments to a drainage system, and waterproofing tapes.
Additionally, proper installation of flashing around edges is crucial to keep water away from vulnerable areas. Ensuring that the balcony has an adequate slope is also essential, as it helps facilitate effective water runoff and prevents ponding.
Incorporating these materials into the finished balcony waterproofing further enhances the waterproofing abilities to safeguard your investment.
Sealants and Caulking
The primary purpose of sealants and caulking is to fill in the joints between materials or around particular fixtures to prevent water infiltration. Specific applications may call for polyurethane, silicone, or acrylic sealants and silicone, latex, or butyl caulking to be applied in a bead and smoothed to ensure a tight seal. The type of joint, expected movement, and environmental conditions dictate the appropriate sealant or caulking for the application. Westcoat incorporates various sealants and caulking within the MACoat and ALX systems to augment the many benefits offered by these waterproofing solutions.
Drainage Systems Installation
Balcony waterproofing methods ensure the structural integrity of valuable external features, which rely on drainage systems to efficiently direct water flow and prevent ponding. During the waterproofing process, efforts may be taken to improve the existing drainage system or introduce a more efficient solution to ensure the longevity of any applied products. Regarding balconies, internal drainage systems — combined with compliant sloping characteristics — can ensure water is redirected to extend the waterproofing’s lifespan.
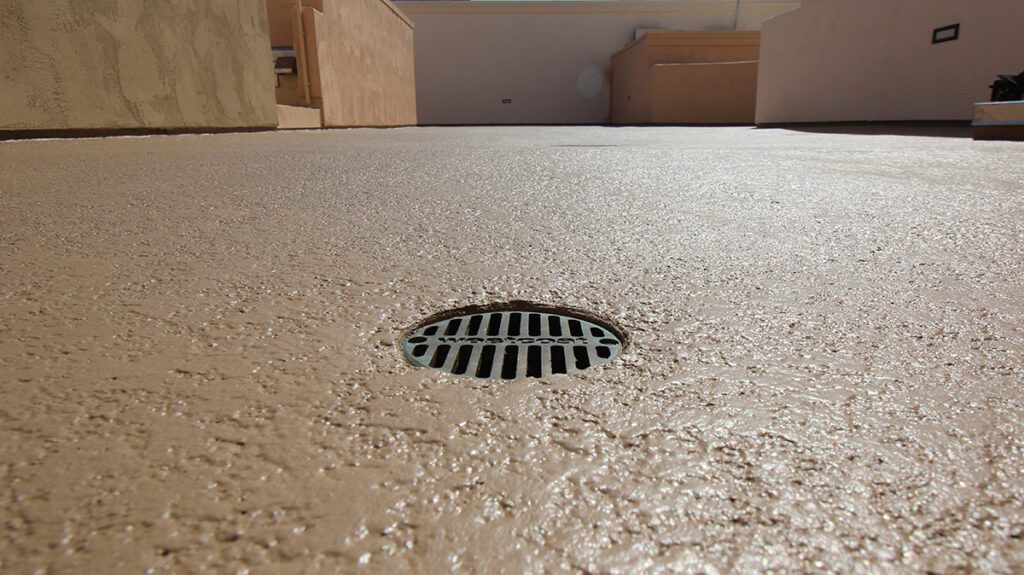
Waterproofing Tapes
Similar to sealants and caulking that shield balconies against water damage, waterproofing tape addresses joints and seams to establish a uniform, watertight layer. Butyl, rubberized asphalt, and self-adhesive membrane waterproofing tapes represent the most common varieties used for specific applications. When selecting the appropriate waterproofing tape, factors such as compatibility, temperature fluctuations, and required durability play a significant role.
Choosing the Right Balcony Waterproofing Method
Well-planned waterproofing methods guarantee a sizable return on one of the more critical investments made by developers, architects, and property owners. Westcoat’s ALX and MACoat full-system waterproofing solutions protect balconies against the damaging effects of water and safeguard the property’s value for many years to come. With the benefits of premium Westcoat products and expert workmanship, property owners can rest assured their assets will be sufficiently protected.
Westcoat supplies high-grade waterproofing and floor coating solutions across industrial, commercial, and multi-family building applications through exceptional products and unmatched customer service. With over four decades of industry experience on our side, we can quickly identify and recommend the best solutions for your project to save you time and money.
Visit our resources section to discover why Westcoat is a trusted name in the waterproofing industry, or contact us at 1-800-250-4519 to speak with our friendly and knowledgeable staff. What project can Westcoat help you accomplish?